Welding
In-House Welding Company
Welding joins every part of the TAB Industries metal fab shop together as a critical step in the cut – form – weld – finish – ship cycle for our fully integrated metalworking center. TAB welders are fully trained experts in MIG welding, TIG welding, laser welding, and other custom welding processes. Our team of skilled craftsmen knows how to apply a strong weld in a smooth, continuous process working with a wide range of materials including steel, stainless steel, carbon steel, aluminum, cast iron, copper, and lead – without warping or distortion – even when joining very thin gauge metals. It takes finesse, experience, and a commitment to top quality. The result is a clean finish with reliable joint strength over the long term every time.
Our in-house welding team incorporates weld procedures based on American Society of Mechanical Engineers (ASME) and American Welding Society (AWS) codes to makes safe, fast, efficient work of parts coming from our laser cutting and fabricating departments. Creating assemblies and complete products ready for powder coating and/or other finishing operations moves quickly with ample capacity to keep up with our laser cutting team and meet tight deadlines every time.
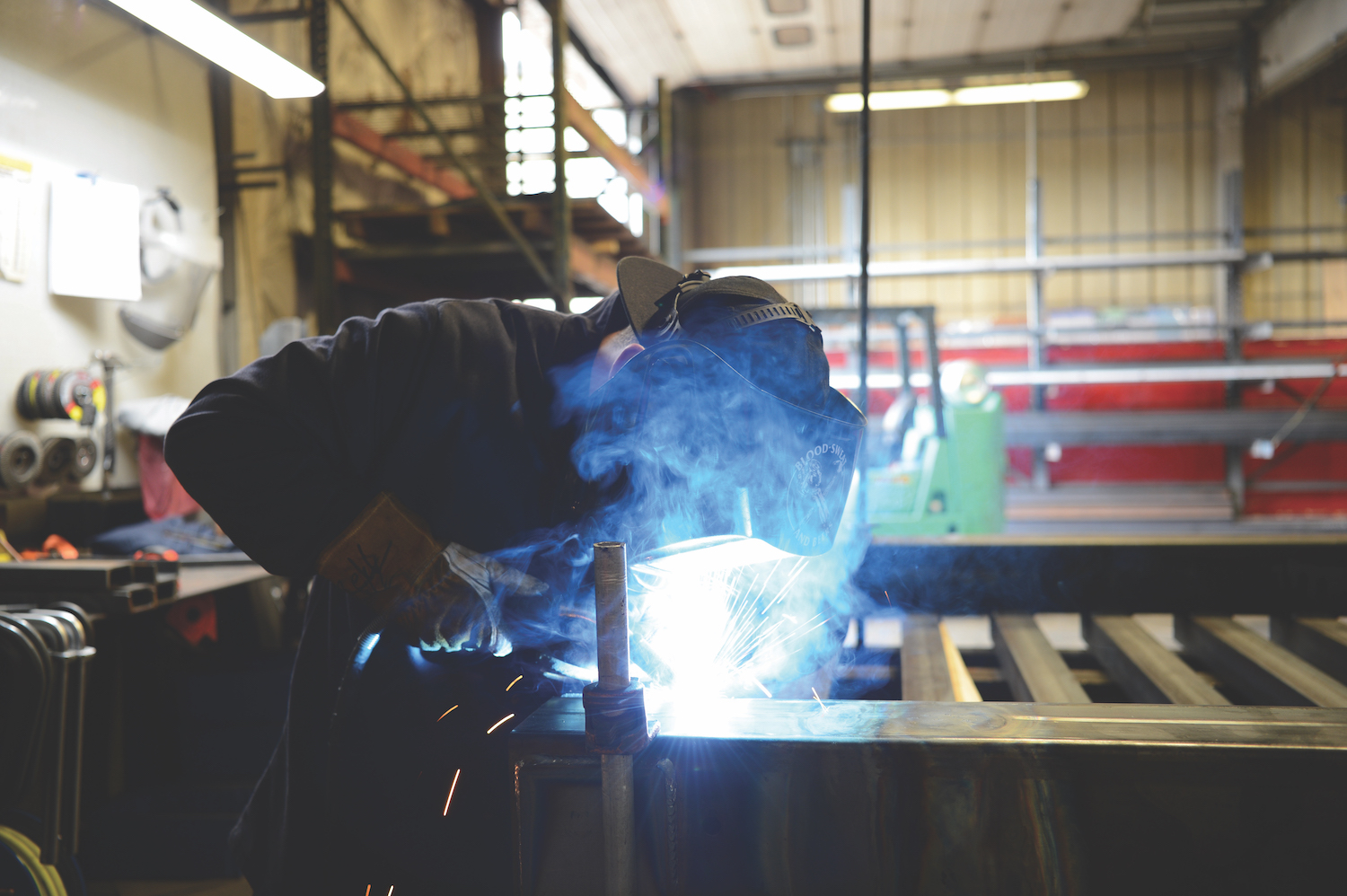
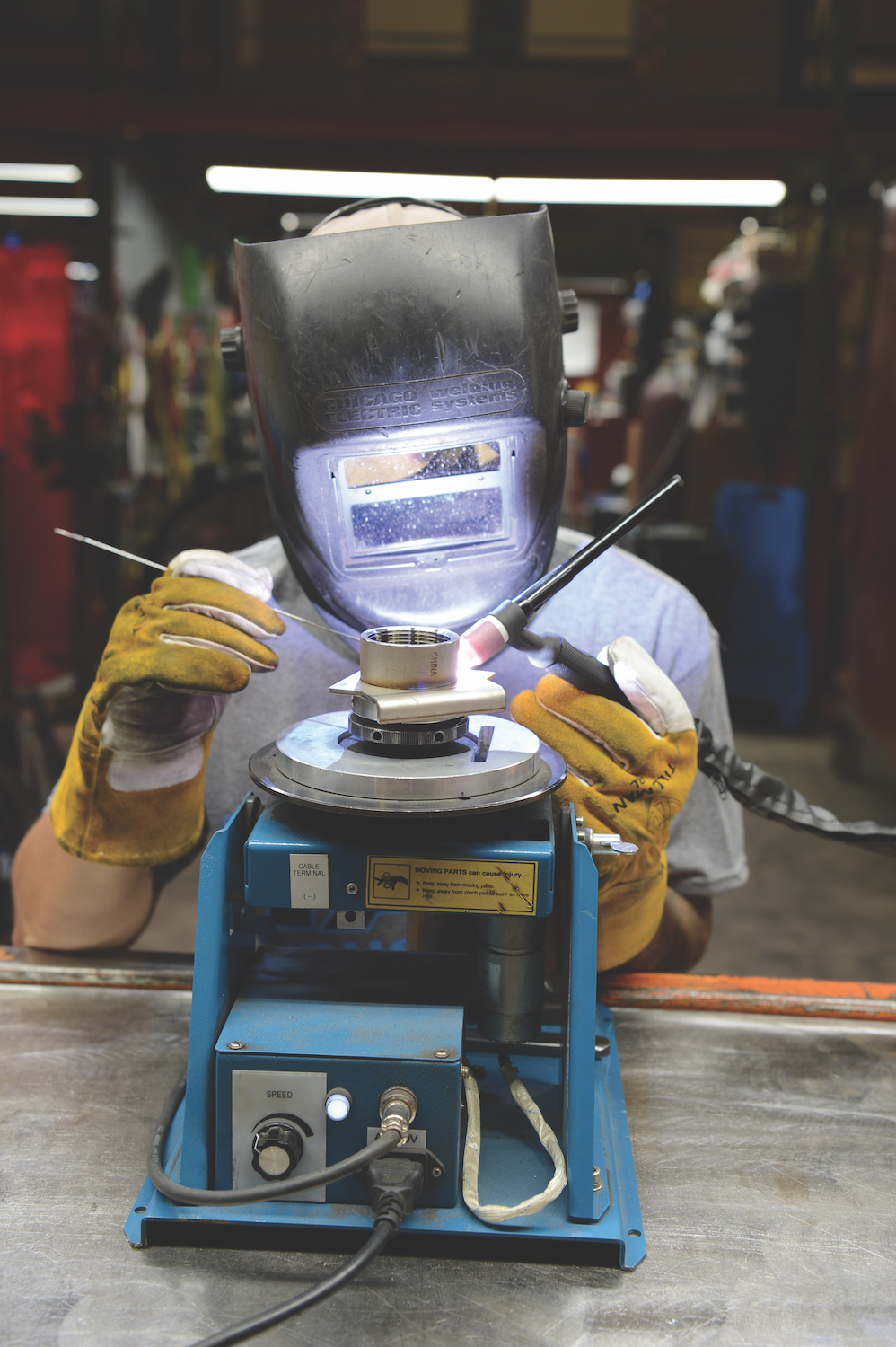
which Welding Process for the job?
Many different types of welding processes are available and each method excels in one or more areas while lagging in others. TAB engineers offer guidance in selecting the ideal welding process for each part or project based on the materials to be joined, the material thicknesses, the deadline, budget, and how the finished parts are to be used, among other considerations. Laser welding may be used for deep welds fusing high precision parts, such as those needed for the aerospace industry, and for intricate or complex parts. Robotic welding is often the choice for automatically producing large quantities of relatively simple parts where the high initial cost of the robot cell can be justified.
MIG welding represents the benchmark for joining two base metals together using a metal inert gas (MIG). This process is used for less complex welds and still comprises the majority of welds performed in America today. TIG welding, or gas tungsten arc welding, is often selected for its wide latitude in material selection and for its ability to maintain the identical level of corrosion resistance as the original material. A skilled TIG welder can consistently produce clean welds in precision shapes with pristine detail.
Welding Experts in Reading, Pennsylvania
Experienced welders will quickly recognize the impressive accuracy, uniformity, and consistent coloration on display in this weld photo. Our lead welder beautifully joined these two aluminum parts using TIG welding.
No cracks, no warping, no oxide formation. We keep our welding stations clean and free of impurities to prevent contamination and assure success each and every time even when welding sensitive, delicate metals like aluminum.
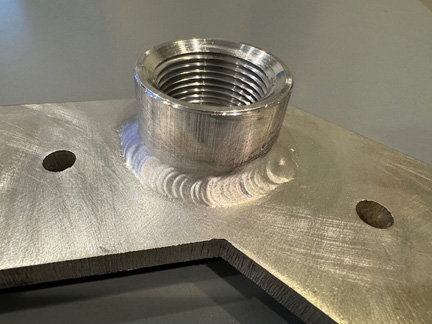